Background of the Technological Innovation
Source: Official Website of Hydro
The aluminum industry has long faced the dual challenges of environmental responsibility and economic efficiency. In traditional aluminum electrolysis, the chemical reaction between alumina and carbon electrodes—driven by electricity—inevitably results in significant carbon dioxide emissions. This not only increases the industry’s environmental burden but has also become a major bottleneck under the growing momentum of global carbon neutrality policies.
In response to this technical constraint, the global aluminum sector has invested heavily in the development of alternative production technologies. Among these efforts, HalZero—a breakthrough innovation developed by Oslo-based multinational Norsk Hydro—offers new hope. With its revolutionary chemical transformation pathway, the HalZero technology presents a promising solution to the aluminum industry’s carbon emissions challenge.
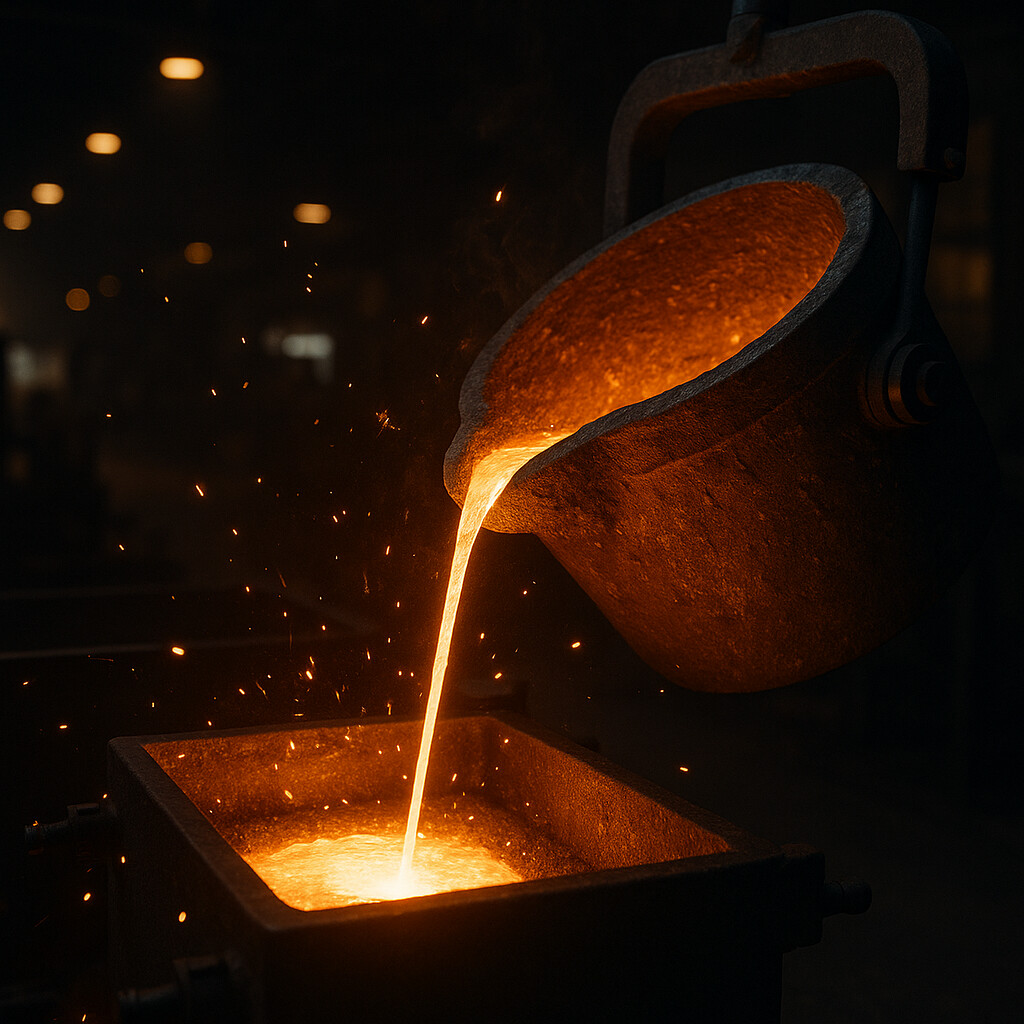
Core Technical Principle
The innovation of the HalZero technology lies in its fundamental redesign of the aluminum electrolysis process. Unlike conventional methods that directly electrolyze alumina (Al₂O₃), this technology first converts alumina into aluminum chloride (AlCl₃), which is then subjected to electrolysis. Though seemingly a simple shift, this transformation marks a fundamental breakthrough.
In this new chemical reaction system, chlorine and carbon materials operate within a completely sealed and closed-loop cycle. This design effectively interrupts the release of carbon into the external environment. As a result, the electrolysis process no longer emits carbon dioxide but instead releases oxygen.
This technological innovation offers the potential for zero carbon emissions without causing excessive energy consumption. Preliminary engineering analyses indicate that HalZero’s electricity consumption is comparable to that of conventional electrolysis methods, providing a critical foundation for its future commercial viability.
Current Status of Technological Development
The HalZero technology has completed its critical laboratory validation phase. The R&D team successfully conducted technical testing and mathematical modeling at their laboratory in Porsgrunn, Norway, confirming the feasibility of this innovative concept.
Building on these initial successes, the project has now entered a more advanced phase focused on scaling up and verifying the technology at pilot scale. According to the current development roadmap, the team aims to produce the first batch of aluminum using HalZero by 2025—a significant milestone in the technology’s progression. They further plan to achieve industrial-scale pilot production capacity by 2030.
To support this roadmap, the Norwegian government, through its state-owned enterprise Enova, provided NOK 141 million (approximately NT$420 million) in 2023 to fund the construction and operation of testing facilities. The total projected investment amounts to around NOK 400 million (approximately NT$1.2 billion), underscoring the strategic collaboration between the government and private sector in advancing breakthrough technologies.
Application Prospects and Challenges
HalZero technology presents a broad range of application prospects. For newly constructed aluminum production facilities, the technology allows for the integration of zero-emission processes from the design phase, aligning with increasingly stringent environmental regulations. For existing plants, HalZero also offers a viable pathway for retrofit and modernization—particularly when replacing outdated production lines—by leveraging current infrastructure and thereby reducing overall upgrade costs.
Nevertheless, the transition from laboratory success to industrial-scale production faces significant challenges. One major hurdle is technological maturity: the stability and reliability of large-scale production must be proven through extended industrial trials. This includes the optimization of process parameters, long-term equipment durability, and the consistent operation of the entire system.
Capital requirements represent another major challenge. Scaling up from pilot testing to full-scale industrial production demands substantial investment in new infrastructure. In addition, the maturation of the technology will require ongoing R&D funding and sustained support from specialized technical personnel.
The Norwegian government’s willingness to invest in the development of HalZero technology underscores the country’s strong commitment to carbon reduction technologies. Although the technology still faces significant challenges before reaching mass production, its eventual commercialization is expected to have a profound impact on the global aluminum industry, particularly in the environmental and economic domains—both of which are of critical importance.
From an environmental perspective, HalZero represents an innovation capable of effectively eliminating carbon emissions associated with conventional electrolysis, thereby significantly reducing the carbon footprint of aluminum production. Economically, the adoption of a zero-emission process would help aluminum producers mitigate the growing burden of carbon taxes and comply with increasingly stringent environmental regulations. As global pressure for carbon pricing, taxation, and regulatory standards continues to intensify, low-carbon production technologies are expected to become a baseline requirement for industrial competitiveness. Enterprises that adopt such technologies early may gain advantages in both technological leadership and brand reputation, thereby strengthening their position and bargaining power within global supply chains.
Viewed from the broader perspective of industrial technological evolution, the advancement of HalZero may become a pivotal turning point in the transformation of aluminum production processes. Moreover, it has the potential to serve as a reference model and practical foundation for other metallurgical and heavy industries seeking to implement green technology innovation.