Join GCM
Welcome to our team!

Employees are our most valuable asset.
We value every employee and strive for excellence through collective effort.
With a stable system and comprehensive benefits, we support our employees in achieving both personal growth and professional fulfillment while contributing to the company’s success.
Great China Metal Ind. Co., Ltd.
Chairman, Mr. Kang Mingli
姜明理
Great China Metal Ind. Co., Ltd.
Chairman, Mr. Kang Mingli
姜明理
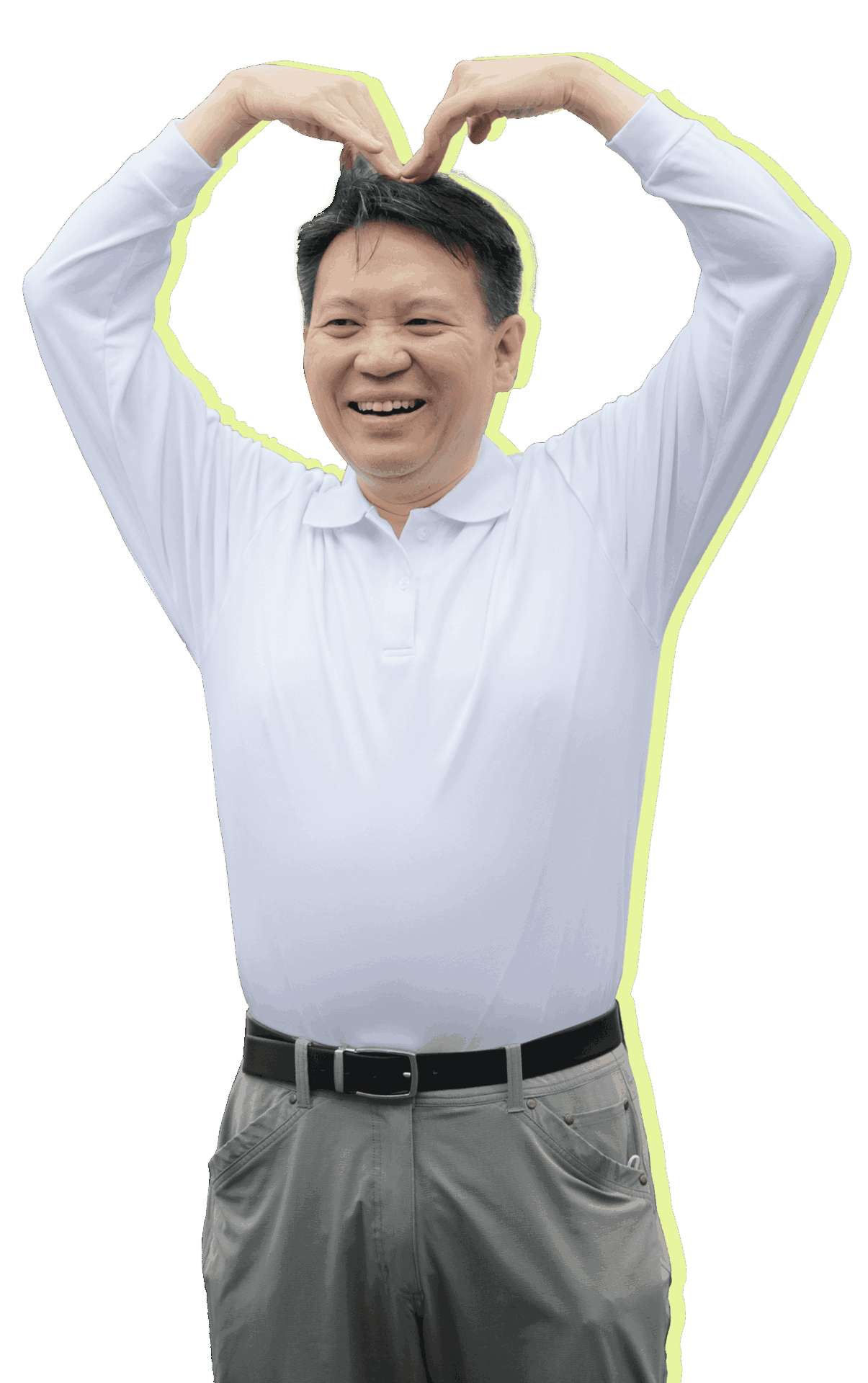
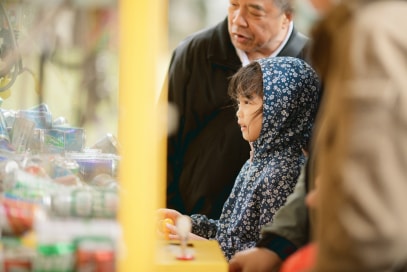
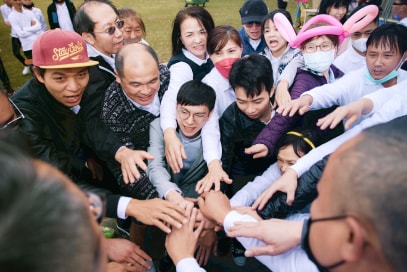
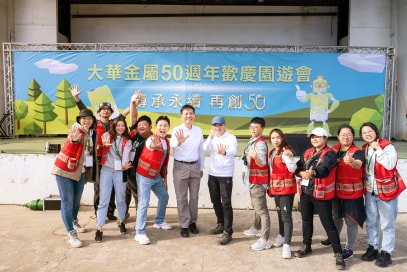
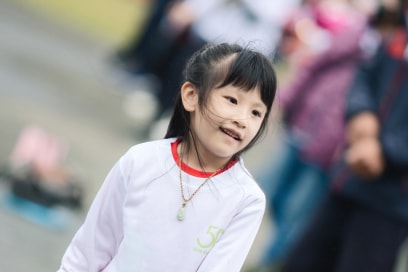
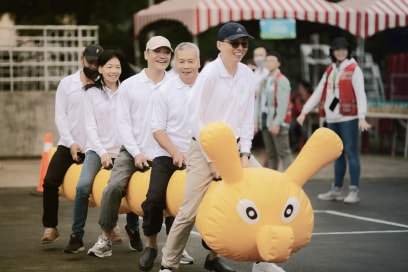
What Do People Say?
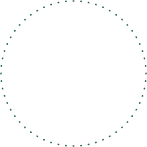
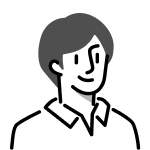
A well-established company specializing in steel and aluminum can manufacturing, actively pursuing digital transformation in recent years, demonstrating a strong commitment to sustainability.
Partner D Company
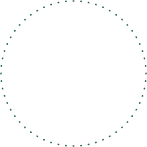
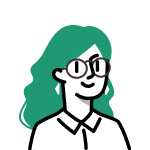
A company that takes corporate social responsibility seriously and prioritizes environmental protection!
Ms. W, Administrative Staff
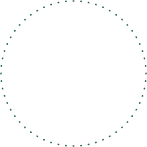
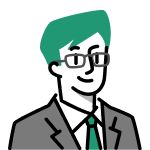
Having worked here for 15 years, I’ve witnessed the company evolve from a traditional apprenticeship system to a structured management framework. I look forward to further progress.
Mr. B, Engineer
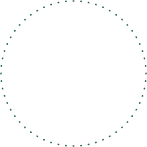
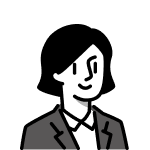
GCM is a professional manufacturer for Taiwan Beer cans—working here means securing a stable job!
Ms. C, Technician
Resources & Benefits
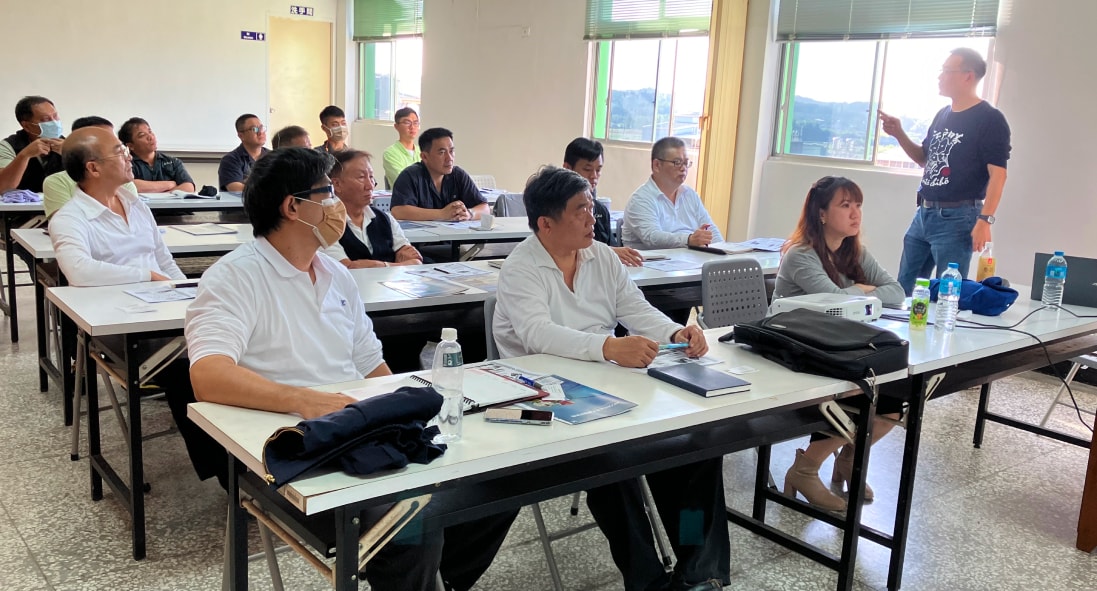
Talent Development & Training
Committed to enhancing talent capabilities and ensuring sustainable business growth, we actively support employee development.
- Onboarding training to help new employees integrate smoothly.
- Job rotation programs to develop versatile skills.
- Regular training and assessments, with promotions based on performance.
- Encouraging employee proposals and skill enhancement through department-specific training programs.
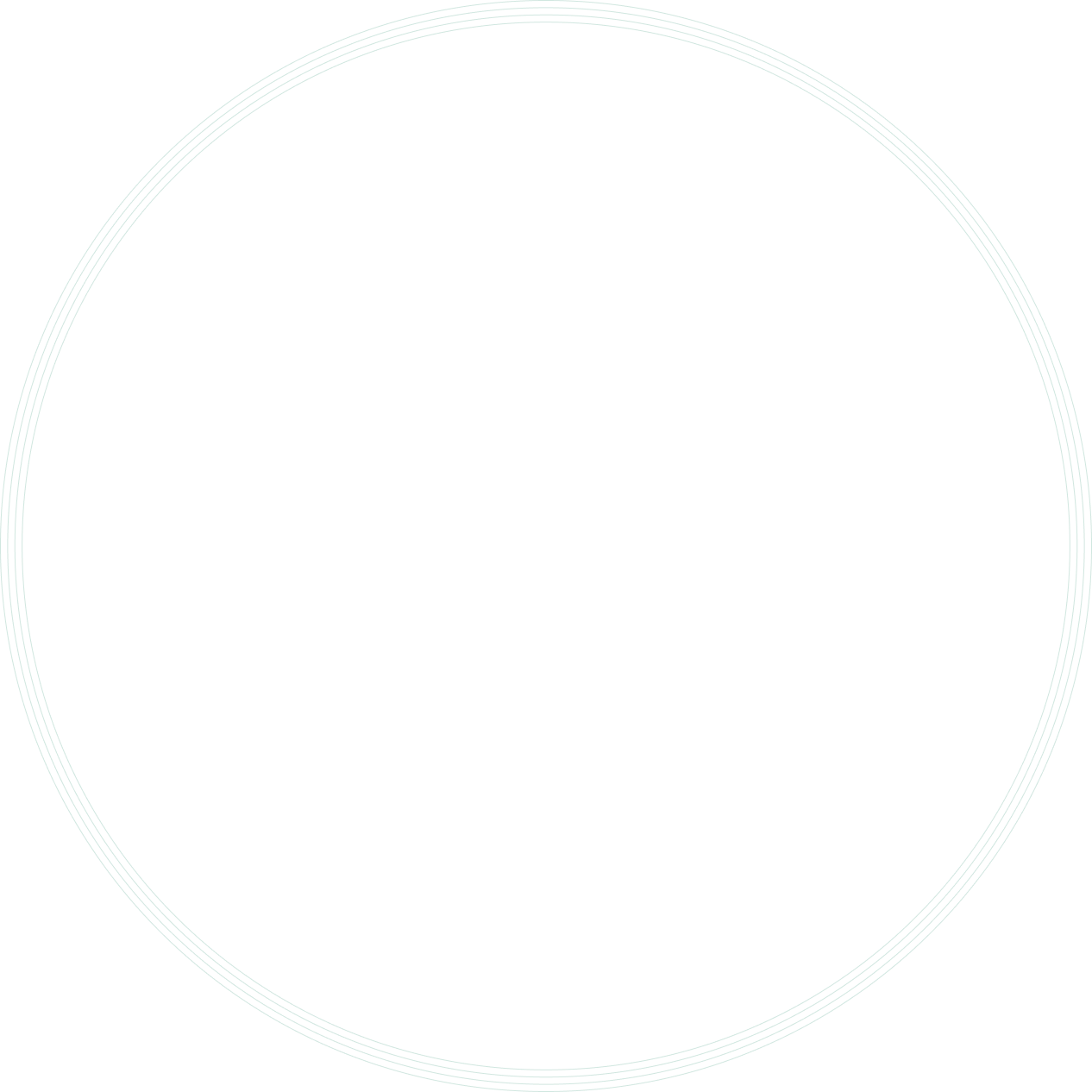
Safety Regulations & Hygiene Management
GCM strictly adheres to international quality and hygiene standards, overseeing the entire process from raw materials, production, inspection, to shipment, ensuring that the products are safe and reliable.
Safety Regulations 1
Machine Safety:
All production equipment is equipped with safety guards and emergency stop devices, with regular inspections and maintenance.
Electrical Safety:
Ensuring proper insulation, grounding, and daily power distribution inspections to prevent electrical hazards.
All production equipment is equipped with safety guards and emergency stop devices, with regular inspections and maintenance.
Electrical Safety:
Ensuring proper insulation, grounding, and daily power distribution inspections to prevent electrical hazards.
Safety Regulations 2
Fire Prevention:
Install fire-fighting equipment, conduct weekly inspections to check expiration dates, and ensure proper functioning.
Formulate a fire-fighting plan and establish a fire emergency response team. Conduct fire drills annually and strictly control flammable and explosive materials.
Material Handling Safety:
The use of handling equipment follows clear guidelines, and employees receive proper training. Stacking heights and transport routes are planned with safety as the top priority to prevent materials from falling and causing injuries.
Install fire-fighting equipment, conduct weekly inspections to check expiration dates, and ensure proper functioning.
Formulate a fire-fighting plan and establish a fire emergency response team. Conduct fire drills annually and strictly control flammable and explosive materials.
Material Handling Safety:
The use of handling equipment follows clear guidelines, and employees receive proper training. Stacking heights and transport routes are planned with safety as the top priority to prevent materials from falling and causing injuries.
Safety Regulations 3
Labor Safety:
We regularly provide safety shoes, uniforms, earplugs, and other protective gear to ensure employees can work in a safe and secure environment.
Emergency Response:
A comprehensive emergency response plan and disaster prevention team are in place to handle situations like fires, earthquakes, and chemical leaks. Regular drills are conducted each year to equip employees with the knowledge and skills needed for emergency situations.
We regularly provide safety shoes, uniforms, earplugs, and other protective gear to ensure employees can work in a safe and secure environment.
Emergency Response:
A comprehensive emergency response plan and disaster prevention team are in place to handle situations like fires, earthquakes, and chemical leaks. Regular drills are conducted each year to equip employees with the knowledge and skills needed for emergency situations.
Hygiene Management 1
Operating Environment:
Regular cleaning and disinfection are carried out in all factory areas. Additionally, to monitor workplace conditions and assess employee exposure risks, we conduct environmental inspections every six months according to our monitoring plan.
Hazardous materials management:
Hazardous materials are stored in designated areas with proper ventilation to minimize risks.
Waste Disposal:
Waste generated during production is managed and disposed of on a scheduled basis to prevent environmental pollution.
Regular cleaning and disinfection are carried out in all factory areas. Additionally, to monitor workplace conditions and assess employee exposure risks, we conduct environmental inspections every six months according to our monitoring plan.
Hazardous materials management:
Hazardous materials are stored in designated areas with proper ventilation to minimize risks.
Waste Disposal:
Waste generated during production is managed and disposed of on a scheduled basis to prevent environmental pollution.
Hygiene Management 2
Personal hygiene:
Employees are encouraged to maintain good hygiene habits. Multiple hand-washing stations are set up throughout the factory, stocked with soap and handwash to promote cleanliness and compliance with proper dress codes.
Health Examination:
We provide annual health examinations for all employees (including foreign workers), covering more than the basic requirements set by Article 17 of the Labor Health Protection Rules. These include general health checks and food-related health screenings. If any abnormalities are detected, contracted medical professionals will provide consultations and health guidance, along with necessary follow-up examinations.
Employees are encouraged to maintain good hygiene habits. Multiple hand-washing stations are set up throughout the factory, stocked with soap and handwash to promote cleanliness and compliance with proper dress codes.
Health Examination:
We provide annual health examinations for all employees (including foreign workers), covering more than the basic requirements set by Article 17 of the Labor Health Protection Rules. These include general health checks and food-related health screenings. If any abnormalities are detected, contracted medical professionals will provide consultations and health guidance, along with necessary follow-up examinations.
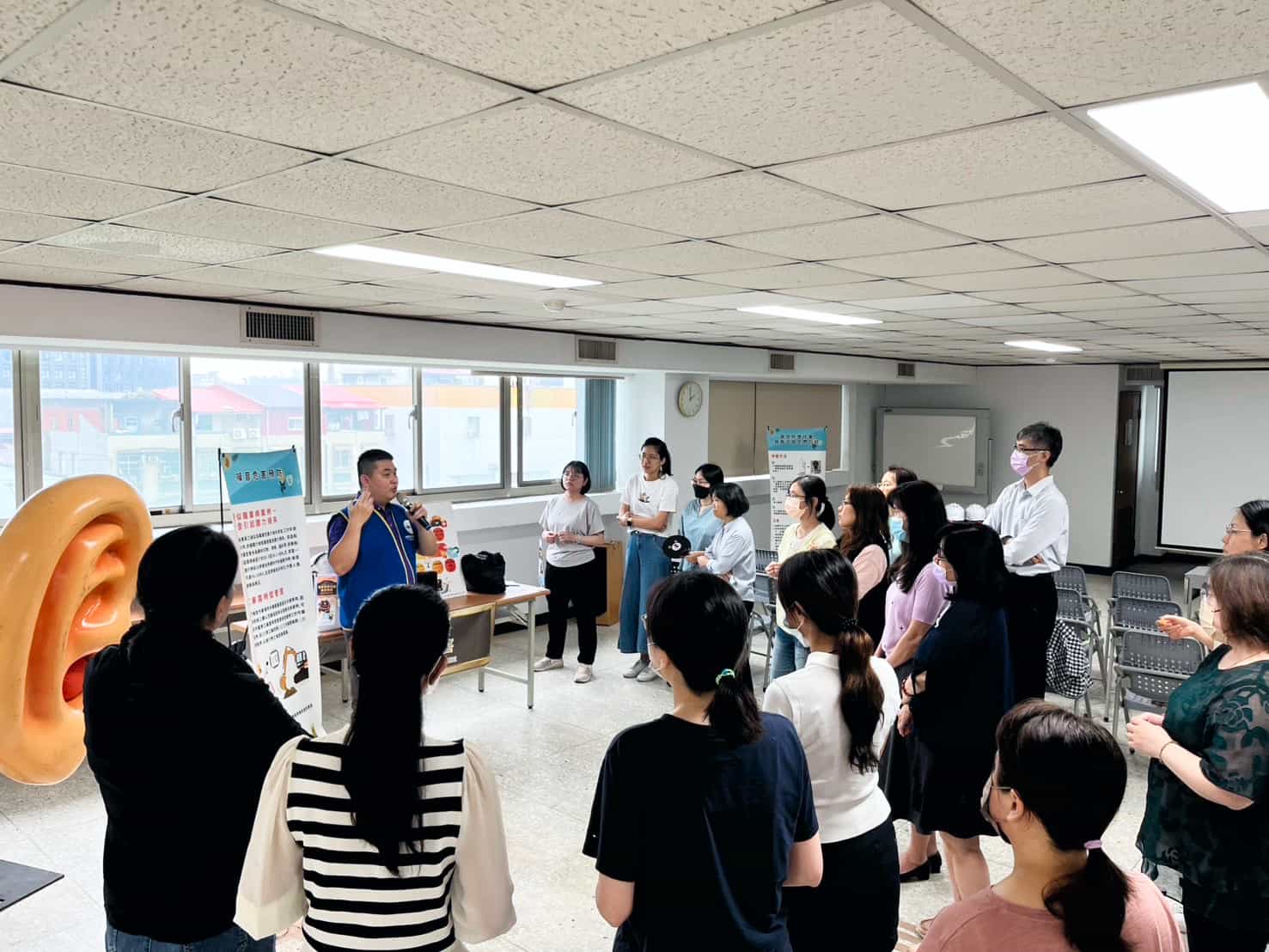
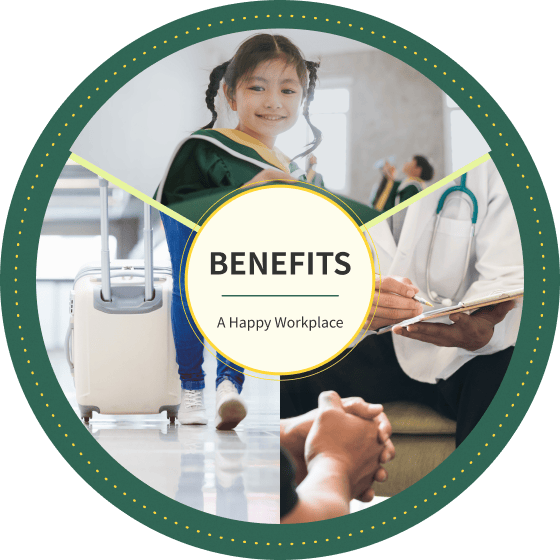
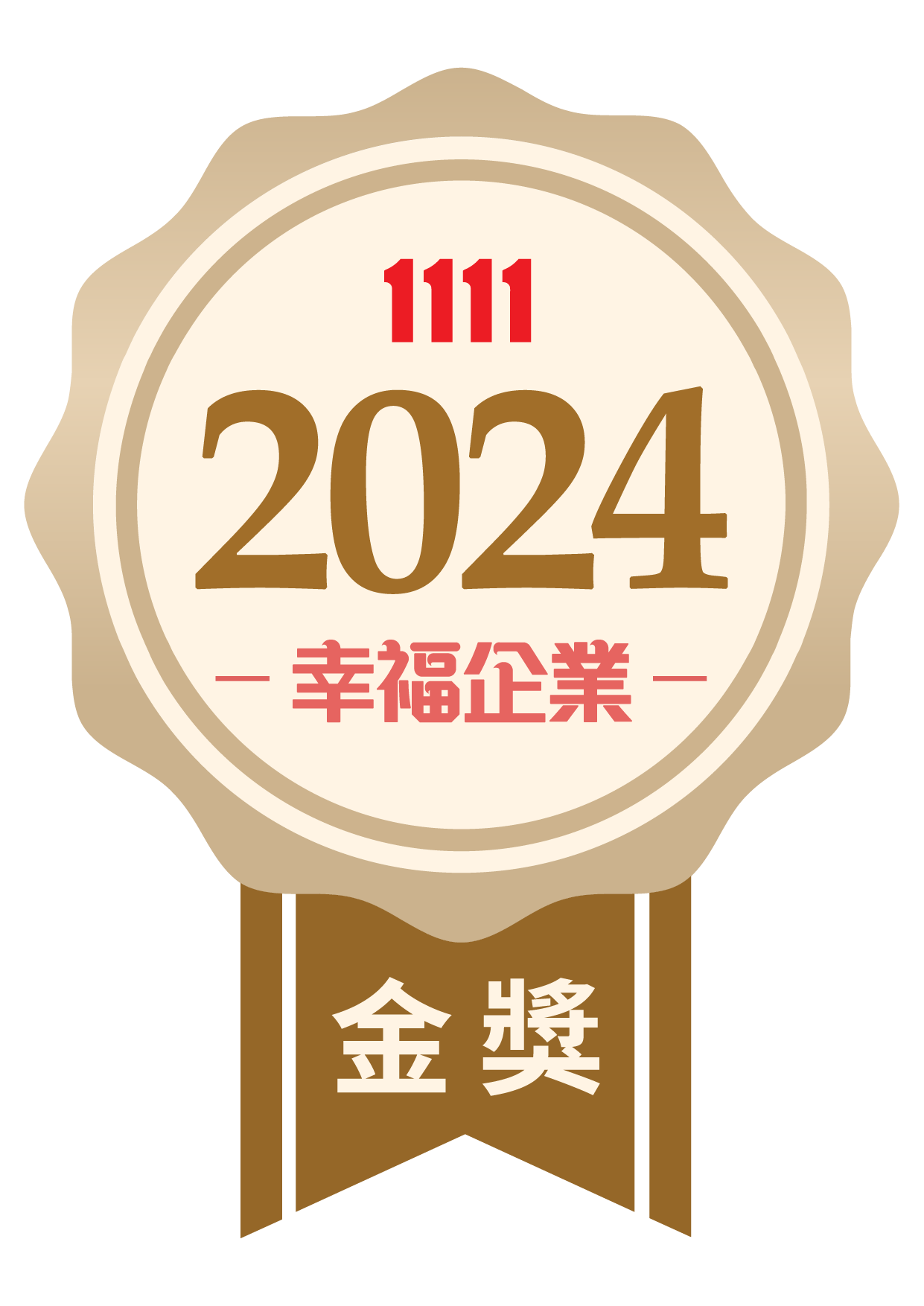
2024 Happy Enterprise
GCM
Bonuses
- Dragon Boat Festival & Mid-Autumn Festival bonus/gifts
- Year-end bonus
- Scholarships for employees' children (elementary to graduate school)
Employee
Well-being
- Provision of labor insurance, health insurance, and retirement benefits.
- Provide free lunch
- Conduct regular employee health checkups.
- Employee development and training programs.
- Provide uniforms for factory employees.
- Financial assistance for weddings, funerals, celebrations, illnesses, injuries, and emergency relief funds.
Work-life balance
for employees.
- Annual subsidies for domestic and international trips.
- Subsidies for self-improvement activities, quarterly social gatherings, and year-end banquets.
- Monthly gift vouchers for employee birthdays.
Workplace
We provide a clean and stable work environment, allowing every employee to focus and work comfortably.
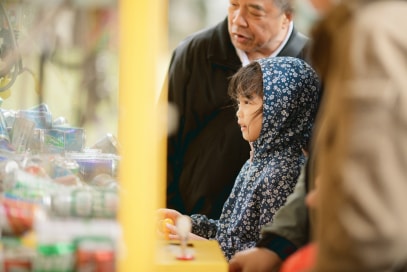
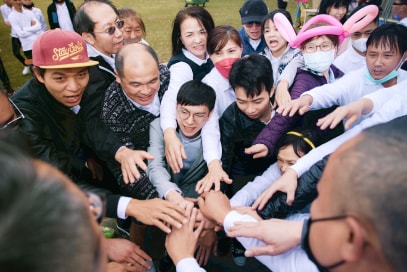
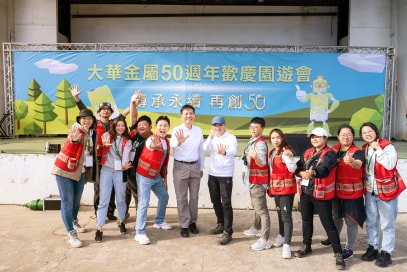
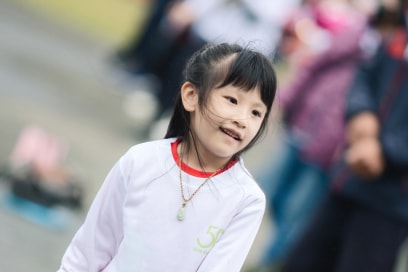
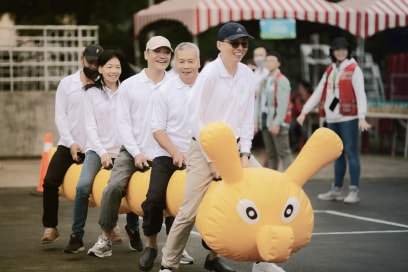