PROCESS
製罐秘辛
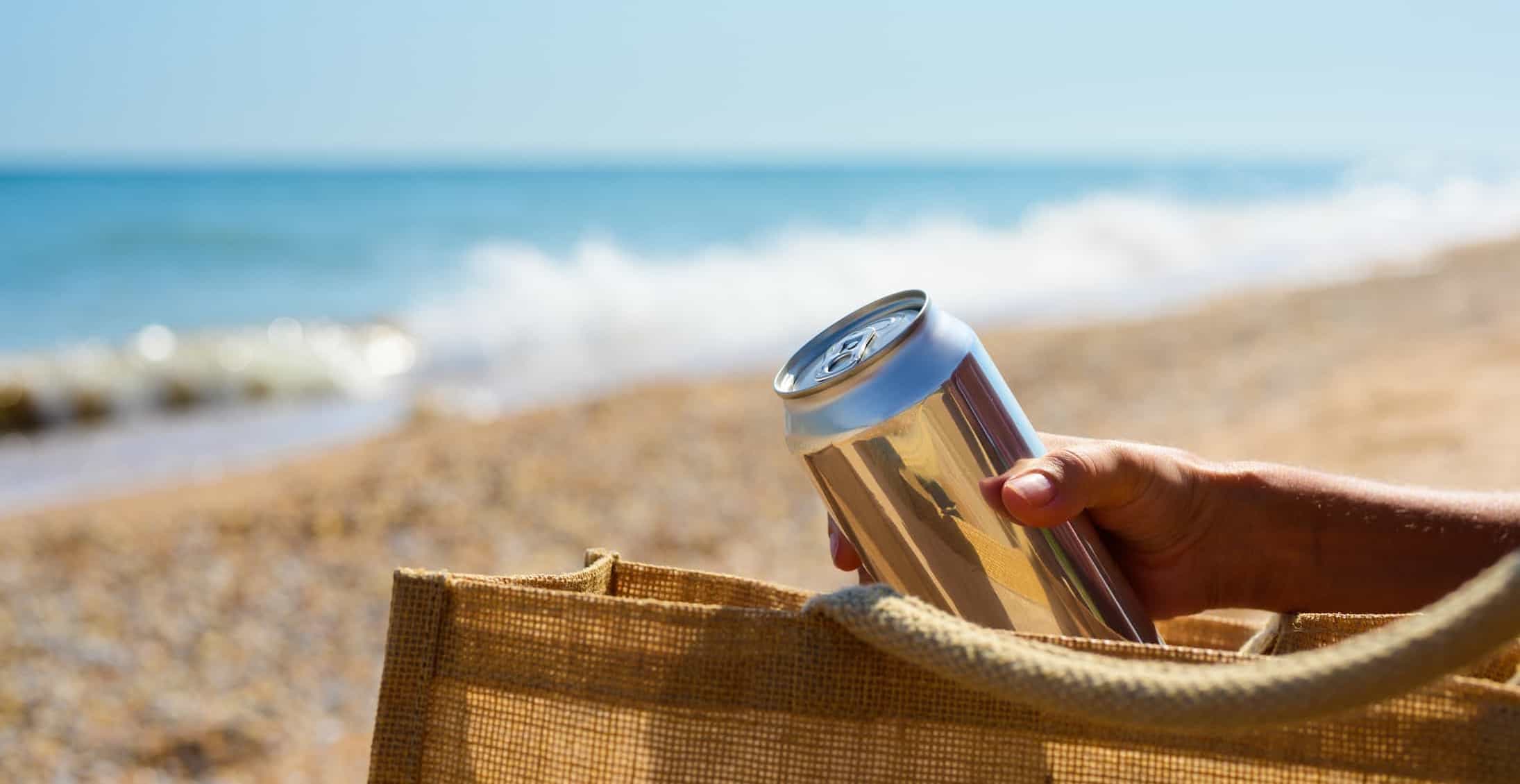
製罐大解析
想知道鋁罐是怎麼製成的嗎?和跟鐵罐又有什麼不同呢?
跟著我們一起揭開鋁罐製造的秘密,探索它從鋁片到成品的奇妙旅程!
跟著我們一起揭開鋁罐製造的秘密,探索它從鋁片到成品的奇妙旅程!
兩片式鋁罐
三片式鐵罐
重複擠壓罐
罐蓋/罐底
環保鋁罐製程
大華在兩片式鋁罐上採用最新的「環保製程」,減少廢水、廢氣排放,期望為地球盡一份心力,達到永續製造的目標。
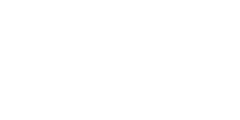
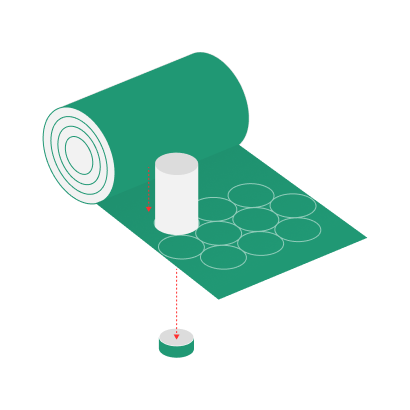
鋁材
沖杯
首先,原材料鋁錠經過熔煉爐熔化,倒入鑄模中冷卻成為鋁鋼坯。鋁鋼坯通過熱軋機進行軋延,逐步形成鋁捲。
製作鋁罐的每顆鋁捲重量達到6~9噸,透過移載設備,進入沖壓機後,便會利用模具沖壓成圓形坯料,再通過拉伸模具進行拉伸,形成初步的杯狀結構(俗稱「沖杯」)。
01
罐身成型
初步成型的沖杯經過多道拉伸工序,逐步拉伸至所需的高度和直徑,在此過程中需要精確控制,避免材料變薄或破裂。
拉伸與修邊
鋁罐的拉伸製程是一個將鋁片或鋁圓片轉變成罐體形狀的複雜過程,它結合了沖壓、拉伸和變薄等技術,透過多次拉伸和變薄,將淺杯逐漸拉伸成所需的罐體高度和厚度。
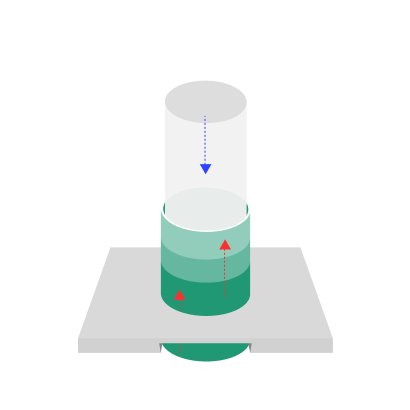
02
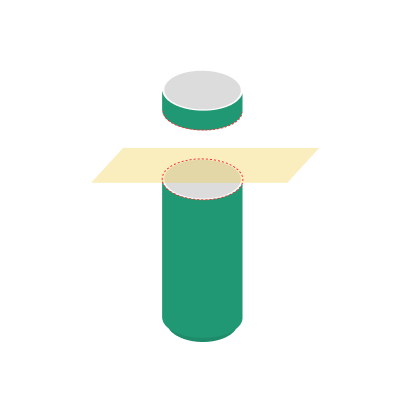
切邊
烘烤整型
完成成型的鋁杯接下來會進行修邊,去除多餘的邊緣材料,確保尺寸精確,並根據需要進行退火處理,以消除加工應力,改善材料性能。
清洗前後的差異
清洗前後的差異在於罐身表面的潔淨度。清洗不僅能去除生產過程中產生的雜質,更能為後續的塗裝、印刷和內面噴塗等工序做好準備,確保產品的品質和安全性。透過有效的清洗,可以提高鋁罐的耐腐蝕性、美觀性和衛生性,延長產品的使用壽命。
環保製程與傳統製程的差異
傳統鋁罐的製造過程中,在拉伸和變薄(Drawing & Ironing)的步驟中,需要使用潤滑油以減少模具與鋁材之間的摩擦和磨損。這些潤滑油會殘留在罐體表面,因此清洗是不可或缺的環節。環保製程鋁罐採用特殊的成型技術,大幅減少了生產過程中對潤滑油的需求,甚至可以完全不使用潤滑油。這使得環保鋁罐在清洗方面與傳統鋁罐產生了顯著的差異。
03
印刷
烘乾
鋁罐印刷製程是確保鋁罐外觀美觀並傳達品牌信息的重要步驟。這個階段需要將設計轉移到印刷板上,並且依照設計製作多個印版,每個顏色對應一個印版。印版製作完成後,這些印版會安裝到印刷機上。在正式印刷前,必須將鋁罐徹底清潔以去除任何油脂或灰塵,確保油墨能均勻附著。當鋁罐被送入印刷機,通過印刷機,將設計圖案逐層印在鋁罐表面,熟練的技術人員此時會確保用色正確,並精確對齊版面以確保最終圖案的清晰度和色彩準確度。
印刷完成後,鋁罐會進入乾燥爐,這一步是為了固定油墨,避免擦傷或褪色。乾燥過程中,鋁罐在高溫環境中短暫停留,讓油墨固化並牢固附著在鋁罐表面。
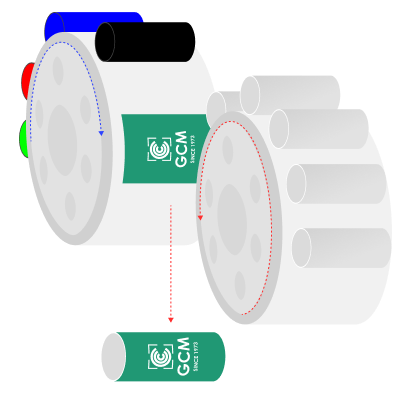
04
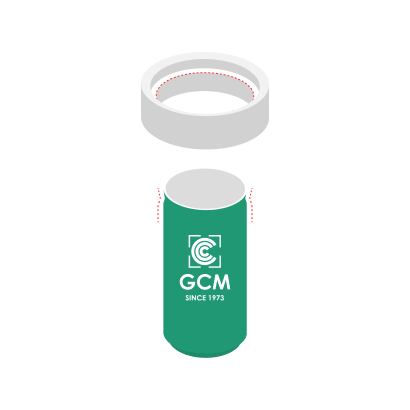
縮頭翻邊
鋁罐縮頭翻邊,是鋁罐製造過程中不可或缺的一環,其目的在於將鋁罐開口處縮小並翻轉邊緣,以利於後續的封蓋,確保罐內產品的新鮮與品質。縮頭與翻邊兩個階段。整個過程看似簡單,但其中涉及許多精密控制與技術。
05
光學、影像檢查
鋁罐會通過光學掃描設備,該設備使用高解析度相機和光源對鋁罐進行全方位掃描,捕捉鋁罐的表面圖像,以檢測任何表面缺陷,如劃痕、凹痕、污染物、油墨脫落或印刷錯誤。掃描後的圖像透過電腦進行處理和分析,並與預設的品質標準進行比較。系統可以識別出有缺陷的鋁罐並將其標記,然後自動將不合格的鋁罐從生產線上剔除,以確保只有合格的產品進入下一個生產階段。
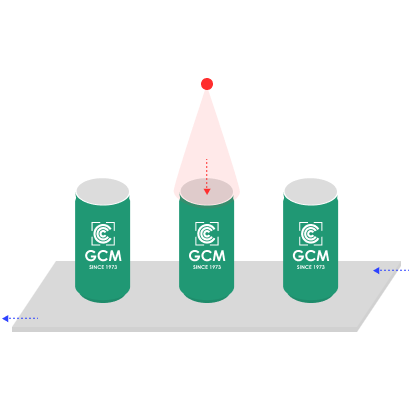
06
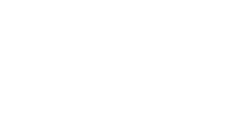
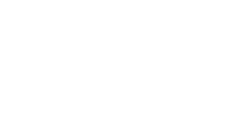
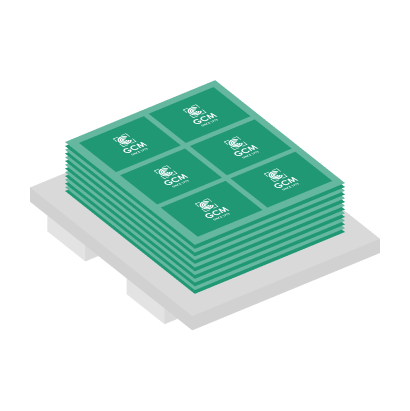
鐵材
印刷
烘乾
三片式鐵罐主要使用馬口鐵作為原料,馬口鐵是一種以低碳鋼板為基材,經過熱浸鍍上一層錫(Sn)而製成的複合材料。根據產品設計,本公司協助客戶印製高品質的各式圖樣,用於印刷罐身、罐底和罐蓋上的圖案、文字和品牌標識。印刷完成後需要接續烘乾油墨,使其牢固附著在罐身表面,防止在後續加工過程中脫落或模糊。
01
裁剪
在三片式鐵罐的生產過程中,裁切是很關鍵的步驟,該程序決定了罐身、罐底和罐蓋的大小和形狀,直接影響到最終產品的品質。本階段會將印製完成的大張鐵皮利用刀模設備裁切成所需長度,裁切的精度和效率直接影響到後續的成型和焊接等工序。如果裁切部件的尺寸和形狀不符合要求,將會導致後續工序的困難,甚至導致不良品的產生。
大華檢驗
確認輪刀間隙以、裁切水平度與垂直度均保持設計公差範圍,是本加工程序中非常重要的重點項目。
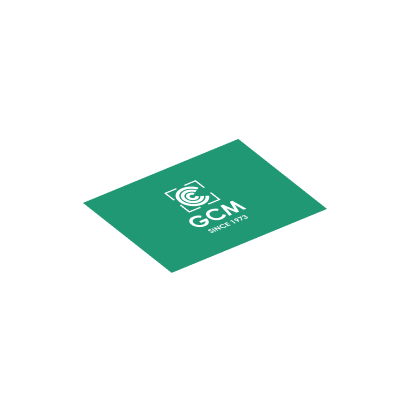
02
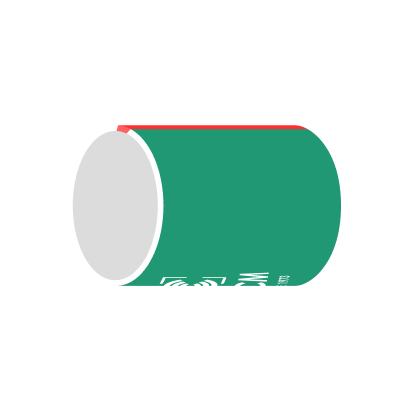
成型焊合
三片式鐵罐的成型焊合是將裁切好的鐵片焊接成罐身的過程。目前的主流技術為利用高頻電流將接縫處熔化,形成牢固的焊接界面。電焊的優點是無鉛污染、強度高、密封性佳。
03
側邊補漆
烘乾
這個步驟主要用於掩蓋焊接縫、增強罐體的耐腐蝕性,並提高產品的外觀品質。補漆層可以隔絕焊接處的空氣和水分,防止罐體內外的金屬發生氧化反應,有效防止生鏽,並延長產品的使用壽命。
製程解析
烘乾
補漆後的烘乾也是一項重要環節,尤其是烘乾參數的設定,例如烘乾溫度過低,塗層固化時間過長,不易乾燥;溫度過高,容易導致塗料變色或開裂。
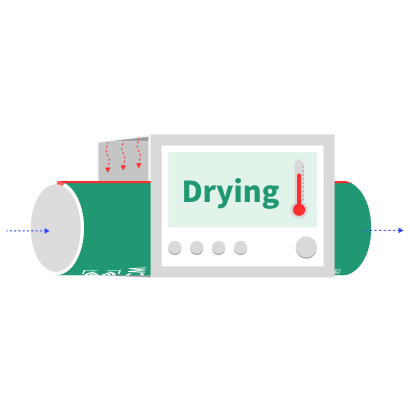
04
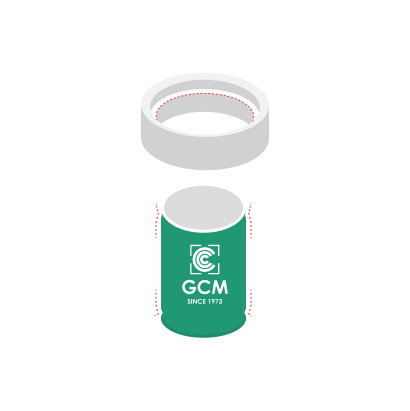
縮頭翻邊
三片式鐵罐的縮頭翻邊是將已經成型並焊接好的罐體,將開口處收縮並翻折邊緣,形成一個可供罐蓋(底)相互進行捲封密合的開口。縮頭翻邊程序對於罐體的密封性、美觀性和強度的建立均十分重要。
補充說明
馬口鐵的厚度會影響縮頭的難度,對於較厚的馬口鐵,可能需要更大的加工壓力。
05
捲封
三片式鐵罐的捲封程序,是將罐身、罐底和罐蓋組合成一個完整的罐體後,對罐口進行封閉的過程。這個程序對於罐體的密封性、美觀性和強度都非常重要,直接影響到產品的品質和保存期限。
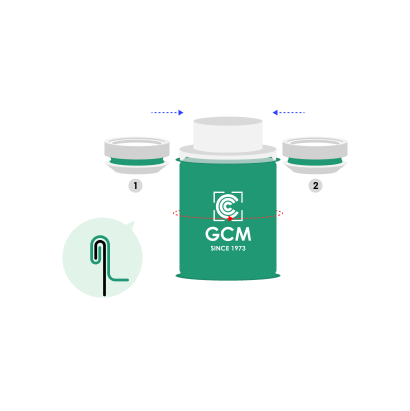
06
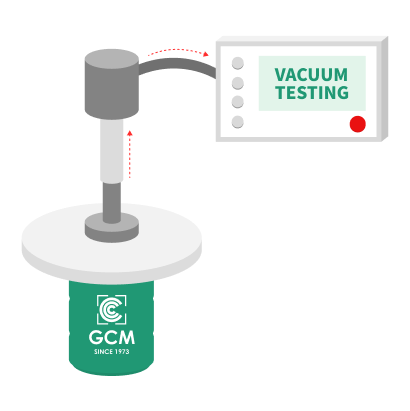
真空檢驗
為了確保罐體的密封性,防止產品在保存過程中發生洩漏、氧化等情況,通過真空檢查可以有效保證產品的密封性,提高產品的品質。
07
罐身補漆
罐身補漆,是為了增強罐體的耐腐蝕性、提高產品的外觀品質,以及掩蓋生產過程中可能出現的劃痕或瑕疵。這個程序通常在罐體成型和焊接之後進行。
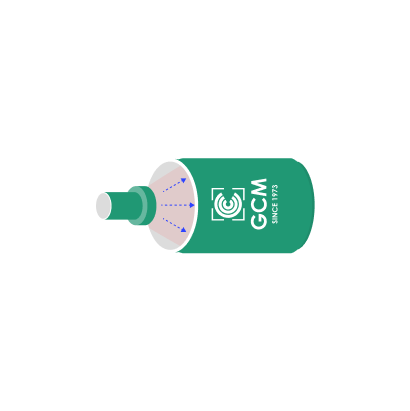
08
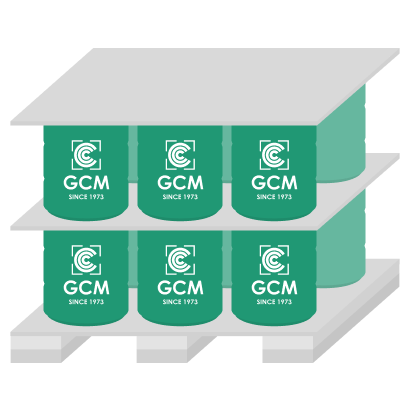
棧板包裝
三片式鐵罐製程的最後一環,便是將完成的鐵罐進行棧板包裝,以利於運輸、儲存和銷售。這個看似簡單的步驟,卻對產品的保護和物流效率有著重要的影響。鐵罐的包裝目的在於防止鐵罐在運輸過程中受到碰撞、擠壓等外力損壞,確保產品的完整性。
09
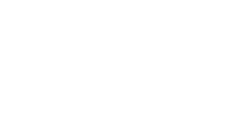
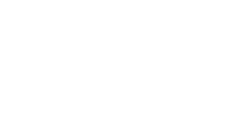
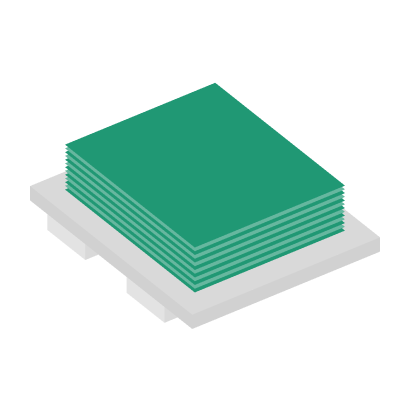
鐵材
兩片式DRD罐(2-Piece Draw Redraw),是一種經過多次拉伸及塑性變型工序製成的鋁罐。其製程的進料程序是整個生產流程的起始,正式生產前必須確認所使用的材料的厚度、成分是否符合生產要求。
01
內外塗漆
塗佈程序的目的是在鐵皮上形成一層均勻、牢固的基礎塗層,根據產品的用途和客戶的要求,選擇適當的塗料,例如如環氧樹脂塗料。
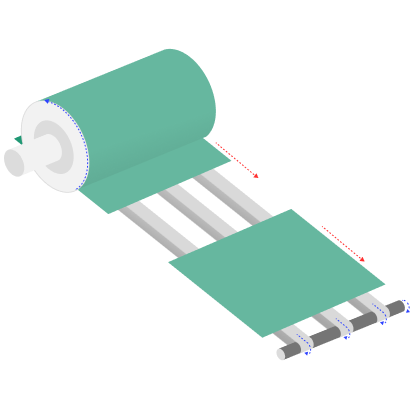
02
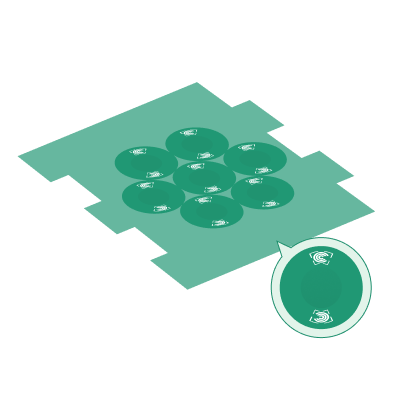
變體印刷
變體印刷是一種在金屬片上印製預畸變影像,透過預測與補償金屬成形過程中的幾何變形程度,於成型後完成預期圖形的方法,是能夠再現拉伸成型後DRD罐圖樣的重要印刷技術。
03
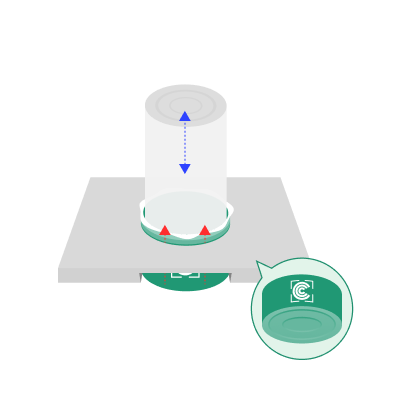
重複擠壓
重複擠壓程序是本製程的核心,將原本平整的鐵片塑造成具有特定形狀和厚度的空罐,由於密封性與結構強度佳,非常適合需要長期保存的食材。
05
修邊
本程序主要目的在於去除罐體邊緣多餘的金屬材料,讓產品外觀逐漸接近設計的樣貌。
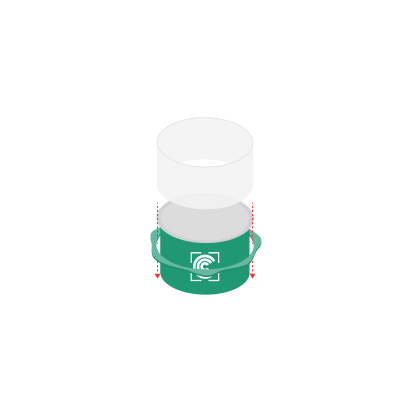
06
光學、影像檢查
透過光學儀器對產品進行非破壞性檢測的一種方法,用於檢測產品的表面缺陷、尺寸精度等項目。通過攝像頭捕捉影像,然後利用影像處理軟體對影像進行分析,將得到的數據與預設的標準進行比較,從而判斷產品是否存在缺陷。
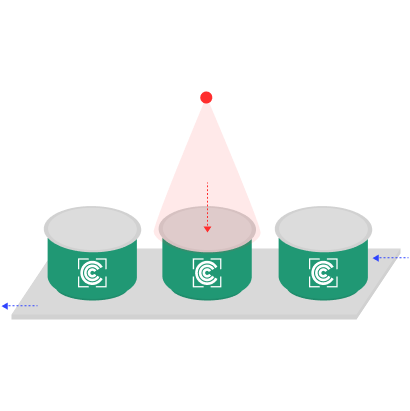
08
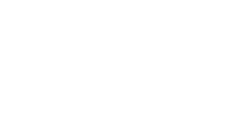
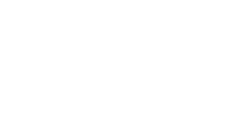
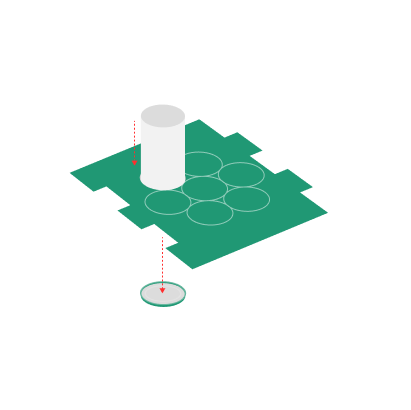
鋁材(鐵材)
沖壓加工
罐蓋所使用的鋁合金需要具備良好的強度、耐腐蝕性以及可塑性。常見的鋁合金包括3003、5182等系列。進料的鋁材(鐵材)需要經過嚴格的品質檢驗,包括厚度測量、表面檢測等,以確保其符合生產要求。沖壓加工是將平整的鋁板通過一系列的沖壓工序,逐步成型為具有複雜形狀的罐蓋(罐底)。
01
蓋肩捲緣
所謂蓋肩捲緣,就是將罐蓋的邊緣向內捲起,形成一個圓滑的邊緣,這個邊緣稱之為捲緣,能提高罐蓋與罐身的結合緊密性,改善密封性能,防止罐內產品洩漏。捲緣完成後,需要進行嚴格的檢驗,包括捲緣高度、寬度、圓整度等,以確保其符合品質標準。
大華檢驗
捲緣後將檢查捲緣外徑、捲緣高度、未捲緣高度與蓋深等規格
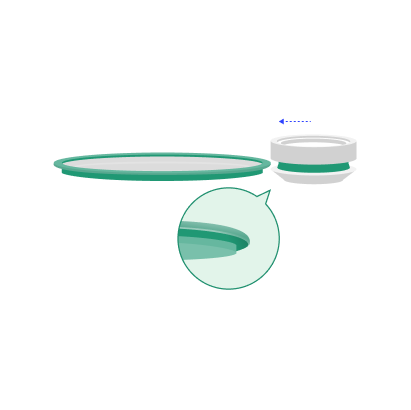
02
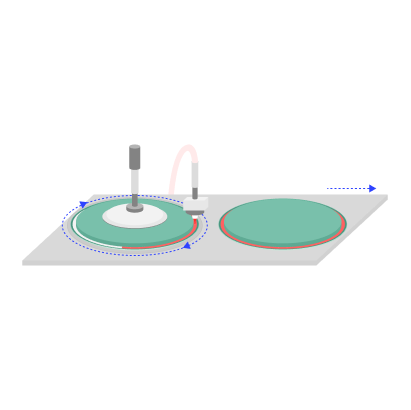
封口膠噴塗
封口膠是罐蓋與罐身緊密結合並保持密閉的重要介質,其性能直接影響到產品的密封性、耐腐蝕性以及保質期。本階段製程係將調配好的膠液利用噴塗設備均勻塗佈在罐蓋的內緣,其噴塗的厚度和均勻度將直接影響封口效果,因此是一個關鍵程序。
03
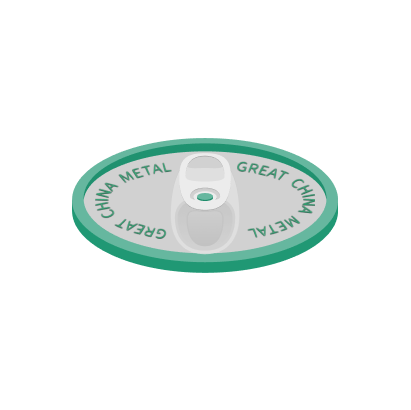
組合沖床加工
組合沖床是一種多工位沖壓機,在一個工作循環中,工件可以經過多個工位,完成多種沖壓工序。每個工位上裝有不同的沖模,負責完成特定的沖壓任務。工件在傳送機構的帶動下,依次經過各個工位,最終形成成品。
05
光學檢查
光學檢查是利用光學原理,通過攝像頭捕捉罐蓋(罐底)的影像,然後利用影像處理軟體對影像進行分析,將得到的數據與預設的標準進行比較,從而判斷罐蓋(罐底)是否存在缺陷。過程中不需要與罐蓋直接接觸,避免對產品造成損傷,其檢測結果也更加客觀,避免了人工檢測主觀性的判定偏差。
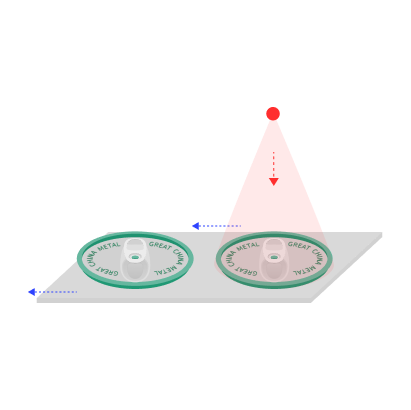
06
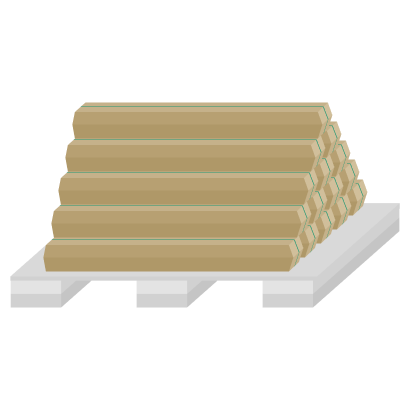
棧板包裝
罐蓋(罐底)製程的最後一步通常是將生產完成的產品進行棧板包裝,以利於運輸、儲存和後續的生產流程。這個看似簡單的步驟,卻對整個生產過程的效率和產品的保護具有重要的作用,良好的包裝可以有效防止罐蓋在運輸和儲存過程中受到損壞,如刮傷、變形等缺陷。
07
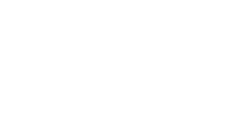