Environmental Sustainability
GCM is committed to advancing low-carbon and environmentally friendly manufacturing processes, striving to become an outstanding enterprise that achieves stable profitability while upholding environmental responsibility. In the face of challenges posed by sustainable development and the low-carbon era, GCM regards energy management as one of its top priorities and a core focus for future operations. In recent years, the company has effectively reduced energy consumption and enhanced production efficiency through diverse strategies—for example, developing low-carbon products using advanced technologies, installing energy-saving equipment such as regenerative thermal oxidizers in its plants, and managing energy use in both offices and production facilities. These various energy-saving strategies are implemented in parallel to achieve comprehensive energy management.
In response to the national timeline for greenhouse gas (GHG) inventory and verification for listed companies, GCM began conducting voluntary carbon inventories in 2023. The company plans to complete GHG inventory processes for its consolidated subsidiaries by 2026, achieve GHG assurance for the standalone entity by 2028, and complete GHG assurance for consolidated subsidiaries by 2029. To meet regulatory requirements on schedule, GCM has already begun reviewing relevant procedures and regulations, and is actively arranging training sessions for internal staff to ensure compliance with government standards and to prepare for future carbon reduction strategies.
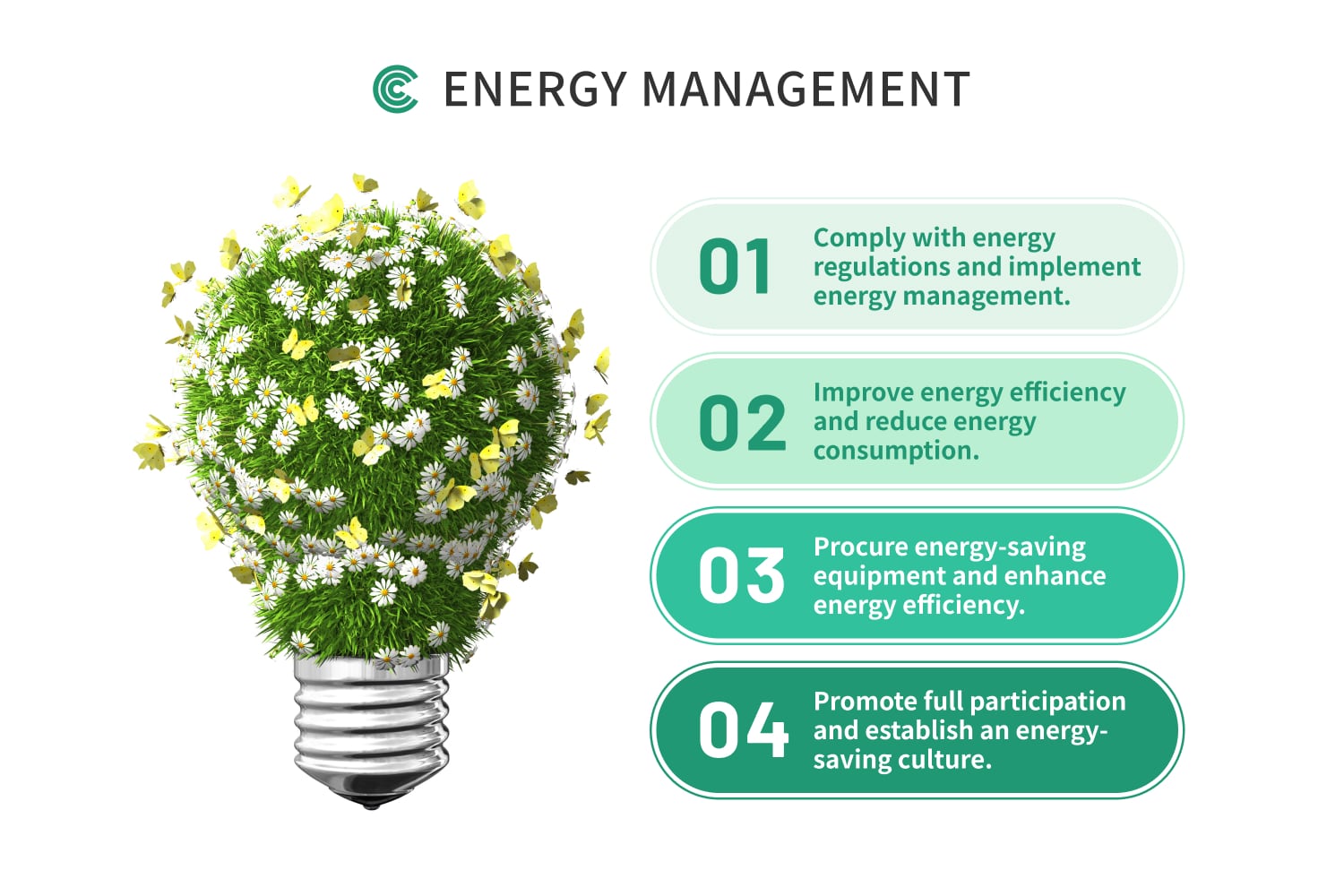
Energy-saving Measures
To achieve its energy-saving goals, GCM has implemented the following measures:
Production Optimization: By streamlining production processes and improving operational efficiency, the company reduces energy consumption and lowers production costs.
Energy-efficient Lighting: Replacement of lighting systems with energy-saving alternatives, such as LED fixtures and timer-controlled lighting, to reduce electricity usage.
Energy Management: Implementation of intelligent energy monitoring and management systems to analyze energy consumption data, detect leaks in real time, and ensure effective energy usage.
Compressed Air Equipment Upgrades: Accelerated replacement of outdated air compressors with energy-efficient variable-frequency drive (VFD) compressors.
Demand Response Bidding: Participation in Taipower’s demand bidding platform to release unused electricity capacity during non-production periods and generate energy-saving profits.
Heat Recovery System Evaluation: Assessing the potential for converting heat generated by factory environmental protection equipment into electricity for internal use.
Energy-saving Awareness: Conducting energy conservation education to raise employee awareness and encourage active participation in energy-saving practices.
Energy Audits: Regular energy audits to assess the company’s energy usage, identify potential energy waste, and develop corresponding improvement measures.
Energy-saving Project Results for 2024
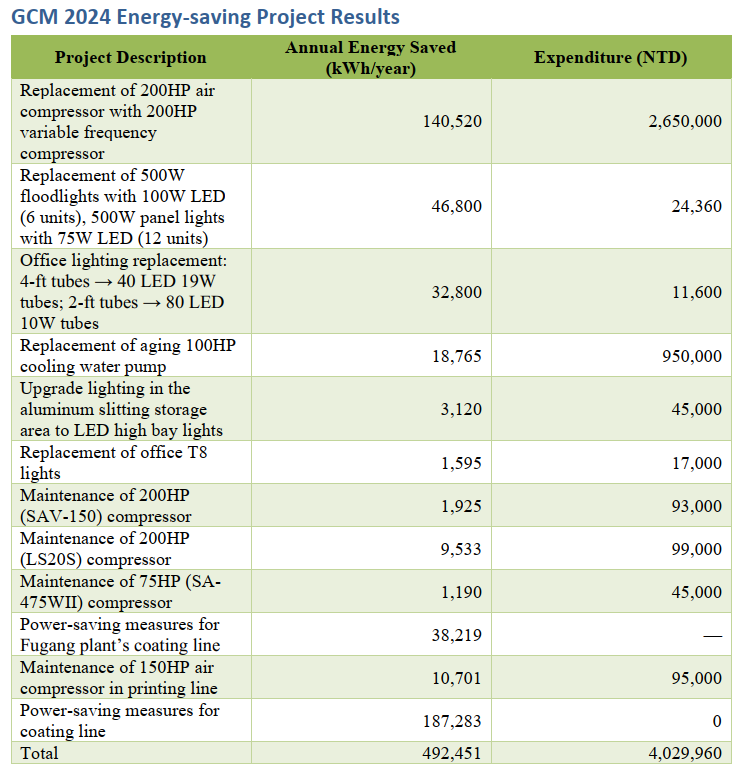
Water resource management plays a critical role in GCM’s operational strategy. We are committed to optimizing water use efficiency in our production processes while enhancing the performance and effectiveness of our wastewater treatment systems. To accurately assess and continuously monitor water usage across all production sites, the company has established a comprehensive water information classification and statistical system. Through detailed data recording and analysis, we can closely track the water management performance of each facility, identify areas for improvement, and continuously refine the efficient use of water resources.
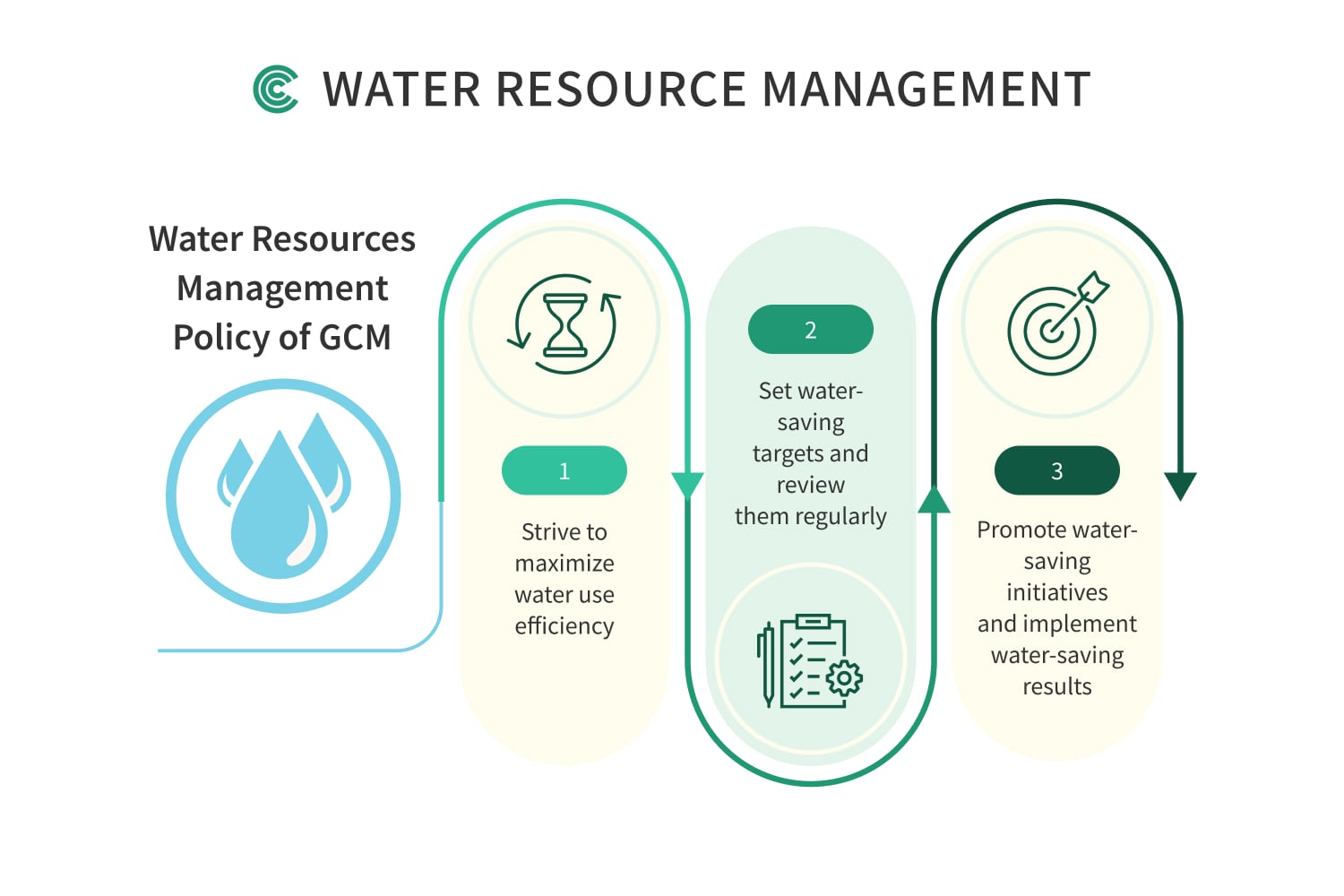
In terms of waste management, GCM conducts annual statistical analyses of waste output and sets targets to gradually reduce the waste generation rate each year, aiming to achieve truly environmentally friendly production. For example, regarding the wooden pallets used in the facilities, the Toufen Plant recycles up to 800 pallets annually, while the Fugang Plant recycles around 495 pallets. In addition, the company employs two dedicated waste management personnel responsible for proper waste classification. All waste is then handled and removed by qualified and certified professional contractors according to its category.
Waste Generation and Reduction
For all types of waste generated, GCM engages appropriate waste disposal contractors to handle the processing. Depending on the waste category—such as industrial waste or general household waste—either the Corporate Procurement Department or the administrative teams at each plant are responsible for selecting contractors and reviewing contracts. This ensures that all waste removal processes comply with relevant regulations.
GCM has always regarded air pollution control as a top priority, recognizing it as a key concern for both internal and external stakeholders. To mitigate the impact of air pollution, we conduct annual statistical analyses of volatile organic compounds (VOCs) emissions and pursue reduction targets through yearly tracking and equipment upgrades.
To meet pollution prevention and regulatory compliance objectives, the Fugang Plant is equipped with thermal exhaust gas incineration systems, which combust production exhaust gases at high temperatures, effectively reducing VOC emissions. In addition, part of the exhaust gas is redirected to the incinerator for secondary combustion, serving as an alternative fuel to reduce overall fuel consumption.
At the Toufen Plant, regenerative thermal oxidizers (RTOs) and manifold systems are installed as part of our air pollution control measures. The RTOs are designed to conserve energy and reduce CO₂ emissions. Exhaust gases are collected via the manifold system and then combusted at high temperatures, achieving a VOC removal efficiency of up to 98%.